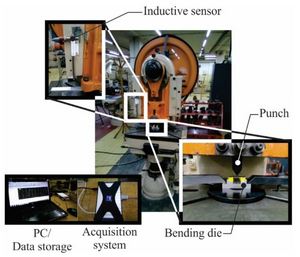
Authors:Miloš Pjević, Mihajlo Popović, Ljubodrag Tanović
Abstract
The parts obtained by sheet metal forming technology can be classified as a percentage in the most common parts of assemblies and sub-mechanisms of mechanisms. The basic problem that occurs when making sheet metal parts using bending process, is the elastic return. The elastic return coefficient that can be used as a correction coefficient in the bending process is necessary to be determine for the used material, as well as for the processing conditions. All this led to high cost of the processing tool. On the other hand, rapid tooling constantly increasing its present in the processing presses. One of the biggest advantages of the rapid tooling is reduction of the cost and processing time of the final product. In this paper, the experimental identification of the elastic return coefficient for three different materials (Al-alloy, non-alloy steel and stainless steel) was performed, as well applicability of rapid tooling on sheet metal bending. The experiments covered a range of bending angles from 65° to 135°. It has been found that depending on the type of material and the bending angle, the elastic return coefficient can vary considerably. It also turned out that its value is significantly influenced by the geometry of the punch. All elements made using additive technology, successfully performed work tasks without the occurrence of destruction.
Key words: Rapid tooling; Sheet metal; Bending; Springback
DOI: 10.24867/ATM-2020-1-005